Industrial Automation
ShareTrends Shaping the Future of the Electrical Sector.
01/11/2024
Case Studies
News & Events
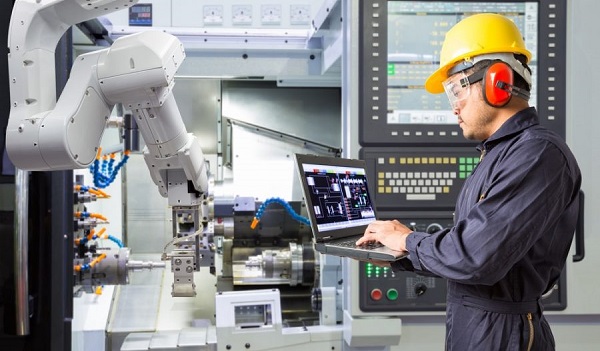
These technologies are opening up new opportunities for businesses to optimise operations, reduce costs and improve safety.
Below are some of the key trends shaping the future of industrial automation as we look ahead to 2025.
1. Artificial Intelligence and Machine Learning Integration AI and machine learning are no longer just buzzwords, they are essential tools in advancing industrial automation. According to Precedence Research, the global AI manufacturing market, valued at $5 billion in 2023, is expected to reach $68 billion by 2032.
In 2025, AI and ML are expected to play an even more crucial role in automating industrial processes. ML algorithms will help detect equipment failures before they happen, reducing downtime and optimising production schedules. AI systems will also be employed in autonomous robots and collaborative systems, allowing them to adapt to dynamic production environments. Industries such as automotive, electronics and pharmaceuticals are already benefiting from these advancements, and their applications are set to expand further.
2. Sustainability and Green Automation
With a growing global focus on sustainability, industrial sectors are looking for ways to minimise their carbon footprints and conserve resources. Green automation is becoming a priority for companies aiming to reduce energy consumption and waste. Automation systems are being designed to optimise resource usage by improving energy efficiency, integrating smart lighting and using energy-efficient motors. Beyond environmental benefits, automation can improve workplace safety by taking over repetitive, injury-prone tasks, allowing workers to focus on more sustainable, long-term roles.
3. Industrial IoT (IIoT) and Digital Twins
The Industrial Internet of Things (IIoT) continues to be a game-changer by connecting machines, systems and processes. By gathering and analysing data from connected devices, IIoT allows companies to monitor performance, track equipment health and optimise production. By 2025, IIoT is expected to be increasingly paired with digital twin technology, which creates a virtual replica of physical assets or systems. According to McKinsey & Co., the global market for digital twins is expected to grow by 60% annually, reaching $73.5 billion by 2027. Digital twins allow manufacturers to simulate, monitor and optimise operations in real time, enabling businesses to foresee potential issues and address them before they become costly. The use of digital twins is especially beneficial for predictive maintenance, reducing downtime, extending the life of machinery and improving overall production efficiency.
4. 5G and the Rise of Smart Factories
The rollout of 5G networks is set to revolutionise industrial automation by enabling faster, more reliable communication between machines and systems. In 2023, global 5G connections surpassed 1.5 billion, according to GSMA Intelligence, making it the fastest-growing mobile broadband technology to date. By 2025, 5G is expected to underpin industrial automation, enabling the rise of smart factories.
Smart factories use interconnected systems that can operate autonomously with minimal human intervention. 5G technology enhances machine-tomachine communication in real time, allowing manufacturers to optimise production schedules, respond quickly to market demands and streamline supply chains. The increased connectivity will also improve data accuracy and enable the seamless integration of IIoT devices, making factories smarter and more responsive.
5. Remote Monitoring and Control
Cloud computing and IoT are enabling businesses to remotely monitor and control automated systems, which is particularly useful in industries with remote or hazardous locations such as mining, oil and gas, or offshore drilling. Remote monitoring allows operators to oversee production processes and perform diagnostics from anywhere, reducing the need for on-site personnel and improving safety. Remote automation systems not only enhance safety but also allow for quicker response times and greater operational flexibility. Businesses can now monitor equipment and optimise production processes remotely, leading to improved efficiency and less downtime.
As automation continues to evolve, businesses have a unique opportunity to increase productivity, cut costs and improve sustainability.
The Middy’s Industrial team is committed to helping you adopt these technologies. Our experts offer end-to-end support, ensuring every part of your project is handled efficiently. Whether you're navigating new automation trends or looking for tailored solutions, we're here to keep your business competitive and drive success.
Contact Middy’s Industrial Team today to learn how we can optimise your operations and support your business.